注塑成型故障排除指南
发布日期:2020/9/11 18:11:48 访问次数:4814
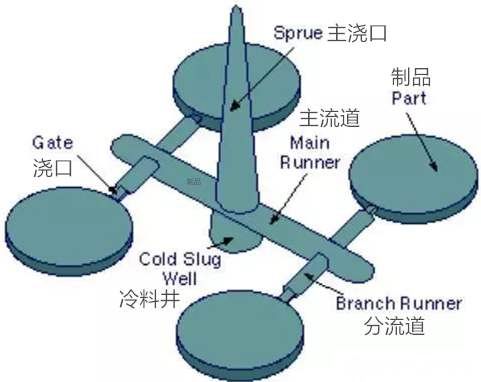
1、 黑点
检查材料是否被污染,特别注意是否使用回收材料。
降低注射压力,减少增压时间。
降低料筒温度避免聚合物和助剂分解,清洗已分解的树脂。
检查喷嘴、料筒内壁、螺杆螺槽和螺杆根部的死角部位,清理已焦化的树脂。
检查注塑机的加热圈和控制系统是否失灵,检查并调整电偶测温点。
2、 BLISTERS(水泡)
3、 BLUSH
4、 制品发脆
检查回料的添加比例。
确定材料含水率在建议范围内,避免材料过度干燥。
提高模具温度,增加制品熔接痕强度。
降低料筒温度,避免材料分解。
减小螺杆转速,降低背压,减小增强级材料中增强剂的性能损失。
制品设计时避免突变的壁厚,尖锐的倒角。
5、 BUBBLES(气泡)
6、 焦化
降低注射速度。
降低注射压力。
增加模具温度。
分析螺杆转速并做相应调整。
降低背压。
检查聚合物在料筒中的停留时间。
检查模具排气孔是否堵塞,在模具烧灼部位增加排气孔。
更改浇口位置或增加浇口尺寸。
使用低压缩比螺杆注塑机。
检查注塑机的加热圈和控制系统是否失灵,检查并调整电偶测温点。
7、 制品开裂
8、 表面分层
9、 变色
降低料筒温度。
降低喷嘴温度。
降低螺杆转速。
降低背压。
检查材料是否被污染。
减少停留时间,缩短成型周期。
检查注塑机的加热圈和控制系统是否失灵,检查并调整电偶测温点。
检查模具排气是否良好。
10、放射纹
降低注射速度。
分析并调整料筒温度。
增加模具温度。
增加浇口、流道尺寸。
11、FLOW LINES
12、飞边
降低注射压力。
降低填充速度。
迅速切换至保压阶段。
调整注射量。
确保材料充分干燥。
检查制品合模线,模具也许已有破损。
调整夹具压力加大合模力。
13、粘模
降低注射压力。
降低注射速度。
减少螺杆前移时间。
分析并调整模具温度。
修正模具缺陷。
使用脱模剂(内、外)。
14、注塑不满
增加注射压力。
增加材料的塑化量保证稳定的余料量。
增加注射速度。
增加增压或高压时间。
增加熔体温度。
增加模具温度。
加大模具浇口或流道尺寸。
增加模具排气孔数量。
在满足制品性能要求前提下使用高流动性的材料。
检查加料口处的材料是否架桥,降低螺杆后段温度,检查加料口的冷却系统。
15、收缩率过大
增加注射压力。
增加注射保压时间和/或保压压力。
增加冷却时间。
降低熔体温度。
降低模具温度。
分析模具浇口位置,如有必要,重新设计浇口位置。
确保适量的余料量。
颜料影响产品收缩率。
16、皮纹
增加注射压力。
增加保压时间和/或保压压力。
增加冷却时间。
降低熔体温度。
增加注射量。
分析并调整模具温度。
扩大流道和浇口以防止材料在充填前固化。
增加模具排气孔数量。
17、银纹
确定材料是干燥的,测试含水率。
检查材料中是否含有污染物。
降低材料在料筒中的停留时间。
降低螺杆转速。
调整背压。
降低熔体温度。
降低喷嘴温度和/或采用较大尺寸的喷嘴。
增加浇口尺寸。
增加模具排气孔的数量。
缺陷 原因 处置
制品脆 聚合物原料含水太高热降解塑化差材料污染 检查含水量可能再需烘干
降低料温和机筒内停留时间
调节背压
排清机筒, 检查料斗
制品不完整 材料粘度太高模具或喷嘴处压降太多空气夹入多模腔时塑料流动平衡不当成型参数不恰当 采用流动性更好的材料, 增加模具和熔化温度以及注塑速度
检查塑料流动的长度/厚度之比
模具排气
检查浇口, 流道和模腔尺寸
增加料量和填料量
增加注塑压力
增加保压时间和保压压力
增加注塑机能力
飞边 模具分型面未完全锁住材料流动态好料量过多 调整锁模力
检查锁模力与制品几何关系
降低熔化和模具温度
减少料量和提前从注塑切换进入
保压
减小注塑速度和保压压力
缩影 在模具中聚合物收缩, 后补的熔化塑料量不足 增加浇口直径
降低机筒和模具温度
增加料量,保压时间和保压压力
增加冷却时间
调整填料量
冷料 喷嘴顶部太冷喷嘴太长 扑捉冷料
检查喷嘴设计
检查喷嘴温度调节系统
增加喷嘴
后退注塑单元
玻纤外露 材料未填塞满 增加填塞
提高模温和注塑速度
延迟从注塑到保压的切换
翘曲 制品各尺寸收缩不同顶出温度太高顶出缺陷模具温度控制差 平衡模具温度
增加注塑速度
检查保压压力
修改浇口(尺寸和位置)
降低模具温度
增加冷却时间
检查顶出系统
修改冷却水通道
明显熔结痕 太高粘度 采用流动性更好的材料
增加熔化和模具温度
改善注塑速度和保压压力或时间
检查注塑系统的设计
烧伤 排气不良 增加排气截面和重开排气
降低注塑速度
延迟切换
表面纹路 粒料中含水太高热降解熔化均匀性差 干燥原材料
降低熔化温度和缩短周期
增加背压和熔化温度
黑点 材料在机器中或热流道中有死角 优化流动, 避免机筒,喷嘴和热流道中的死区
颜色变化 热, 氧化降解塑化差含水量高 缩短熔化驻留时间和降低温度
检查色母的成份
增加背压和降低螺杆转速
干燥原材料
收缩 改进注塑参数 降低熔化和模具温度
提高保压压力和时间
延迟切换
表面粗糙 塑化有问题材料污染 提高熔化和模具温度
增加注塑速度
检查是否有外来的粒料以及再粉碎料的尺寸
冲击痕 浇口设计不合理 重新放置浇口位置或修改其尺寸 (宽/厚度比)
修改浇口, 使熔化料流到模腔壁处, 从而有规则流动
周期太长 材料结晶速度慢冷却时, 模腔和制品间的热交换差 换一适当的材料
减小料把直径
检查或改善冷却水道
降低模温
气泡 粒料含水塑化差 加工前烘干
增加背压和降低螺杆转速
空孔 防止由于厚部位, 加筋和凸出部位的收缩, 产生的模腔中材料不足 增加料量, 降低螺杆转速
调整注塑压力和注塑时间
调整填料量
调整温度设置, 也许过高
分层 材料污染 排空料筒
顶出有问题 制品留在模腔中 降低制品致密
改进脱模顶出系统
增加冷却时间
消除模腔坑凹和粗糙
增加模腔壁上的脱模斜度
增加顶针数量和其直径
流动线 熔化和/或模具温度太低 增加流动速度
流涎 材料流动太好 降低喷嘴和熔化温度
采用合适的喷嘴
塑化结束时略加后拔
干燥原材料